Our powder to part lab
Your co-engineering partner, innovate with us.
A laboratory open to innovation
ArcelorMittal has been producing Steel Powder in a pilot atomizer in its additive manufacturing laboratory in Avilés, Spain, since 2018. In our dedicated R&D facility and with more than 50 full-time researchers, we have developed a comprehensive understanding of the relationship between the different alloys, the atomization parameters, the parameters of the Additive Manufacturing process and the final properties of the printed parts.
ArcelorMittal believes that Additive Manufacturing can create new opportunities for all types of industries, enabling the production of complex, customized parts with improved properties, while reducing material waste. With our participation in the Additive Manufacturing market and, reflecting our successful approach with our S-in motion® program in the automotive sector, we aim to scale our Steel Powder offering in collaboration with customers and industrial partners, with joint designs and collaboration in engineering projects.
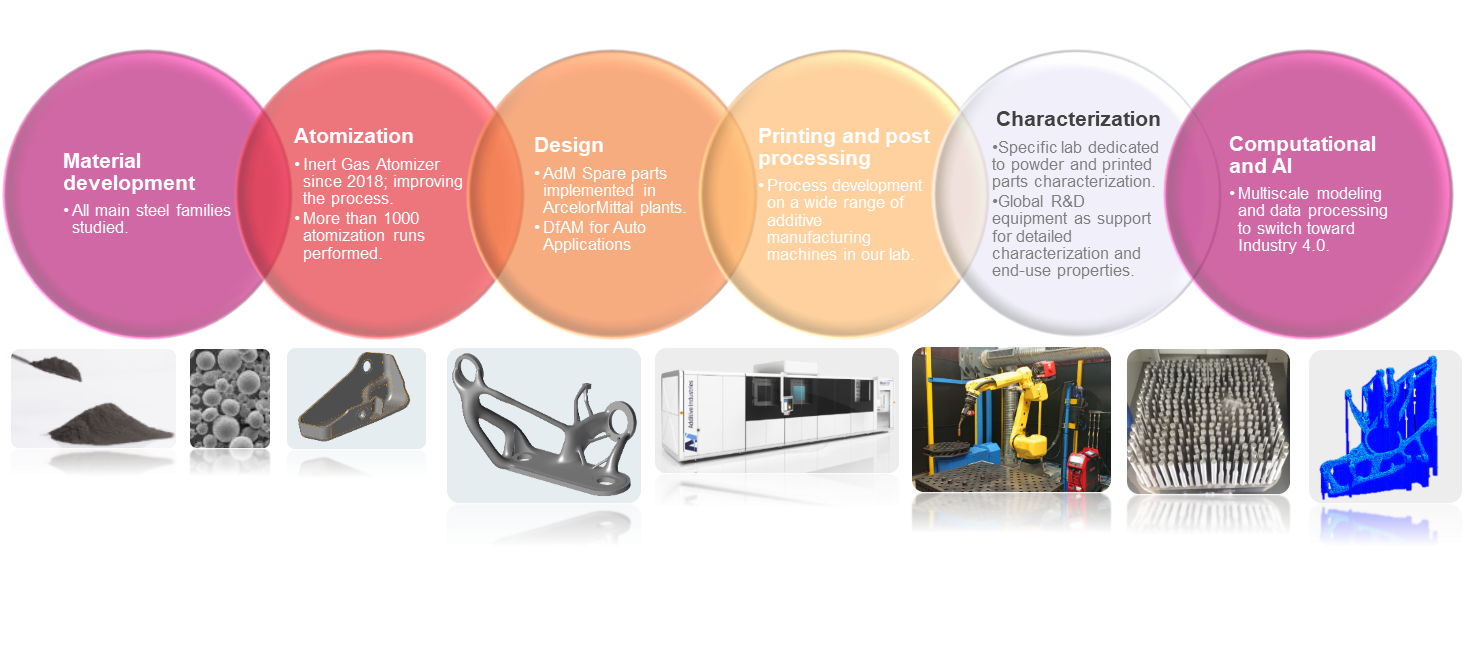
Ability to support development and testing cycles in our pilot atomizers and our characterization laboratory.
- Our pilot atomizer 1.0 is intended for internal development to create our own alloys and optimize our manufacturing process.
- The pilot atomizer 2.0 has a customer focus that can help us with developments for specific applications or atomization on demand.
- Our metallurgical laboratory supports to clients for new developments.
We have a complete metallographic laboratory that has a Precision Saw, Wet Abrasive Saw, Assembly Presses, Grinding Machines, Polishers, Vacuum Dryers and Ovens and light optical microscopes. The laboratory is specialized in the characterization of both Steel Powder and printed steel parts (with the capacity to perform hardness and tensile tests).
In addition, the laboratory is complemented by our global network of R&D centers (in Europe and America), which allows us to replicate most traditional methods of destructive and non-destructive testing of materials and parts. ArcelorMittal Global R&D has 1,600 researchers worldwide spread across 14 geographic locations, always working close to our customers and our own facilities.
Design and modification for Additive Manufacturing in steel
For two decades, in our R&D centers dedicated to the automotive industry we have accumulated considerable experience in designing solutions in conventional steels to help our customers, always taking into account the application and the final part and ensuring that The properties of the steel were taken into account to offer the best performance.
Our additional experience in the Additive Manufacturing of thousands of spare parts for our own operations allows us to know and exploit the full potential that can be achieved with our Steel Powder.
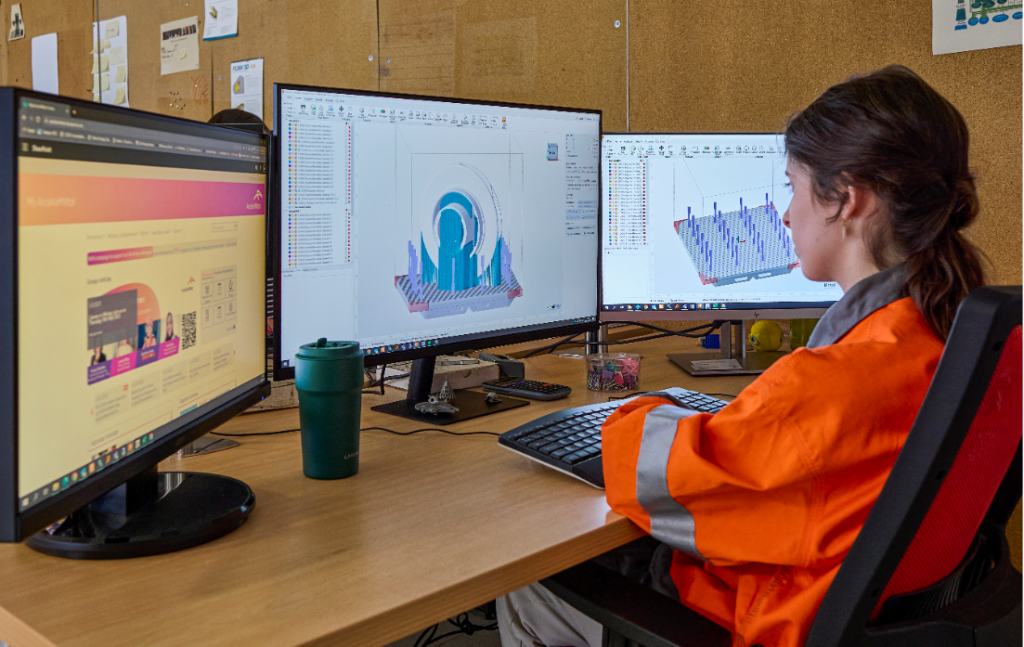
Printing and post-processing
We all want to make the most of existing equipment and machines, taking full advantage of the possibilities that Steel Powder printing offers. That is why our designs simulate, optimize and test the parts in what would be real conditions of use.
This allows us to optimize print parameters, process window and laser path, which will then be applied to the production of our own in-house spare parts – a service that is now available to support our customers.
Contact us to find out the capacity of our laboratory available for different printing and post-processing technologies and sizes.
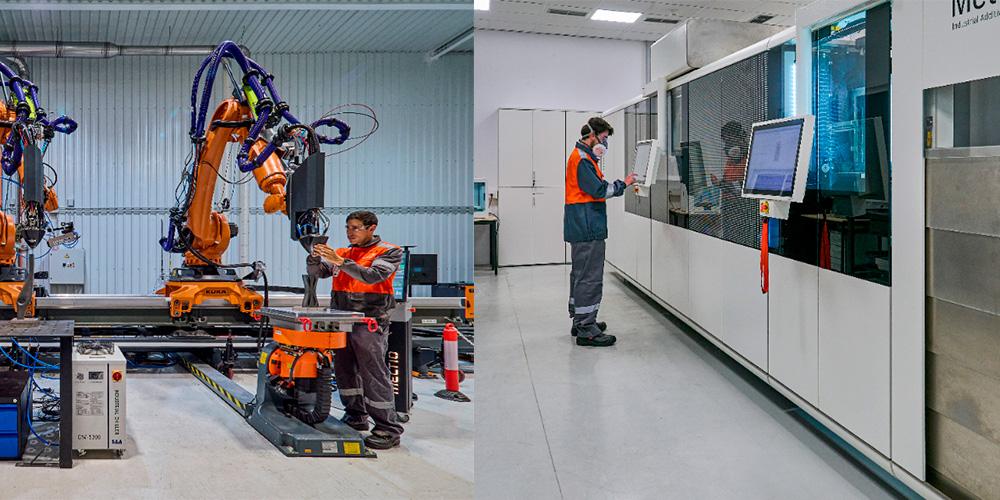
Solutions to reduce fine particle emissions from brakes: let's talk about the Euro 7 regulation
The Euro 7 regulation, which will come into force in 2025, aims to reduce vehicle particle emissions by 27%, up to a maximum of 7 mg per kilometer. This poses a significant challenge for the automotive industry, as brakes are the main source of fine particulate matter in new vehicles, now that previous regulations have significantly reduced powertrain and exhaust emissions.
One of the most promising solutions to achieve this goal is to apply a hard coating to the brake discs, using a wear-resistant material applied to a conventional iron brake disc. The coating process can be performed by high-speed laser or cold spray, using a mixture of carbide and stainless steel powder.
ArcelorMittal Powders' Steel Powder range includes standard solutions that have been selected by leading automotive OEMs for their performance and durability.
Continuing our tradition of improving and innovating to meet the changing needs and challenges of the industry, we have created a laboratory to replicate the coating process and develop further Steel Powder solutions that will optimize both the coating process and the final coating properties. , thus achieving the best results in reducing brake emissions.
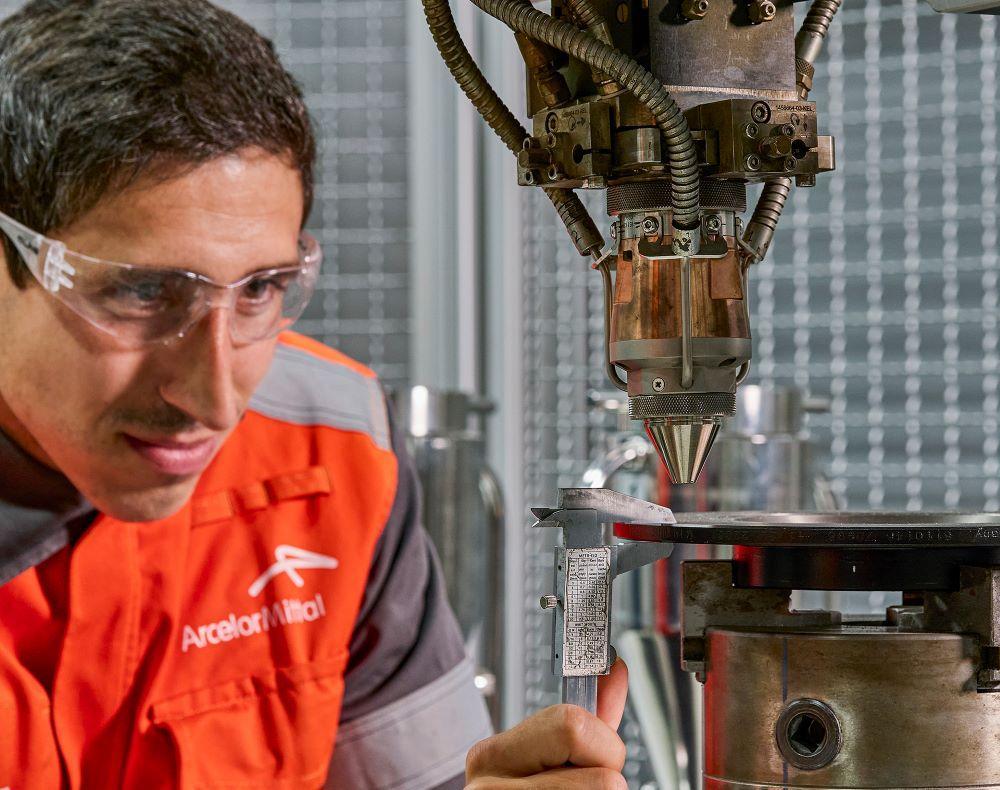
Do you need advice?
Contact our experts to find out how we can help you choose the material that best suits your production needs.