Automotive
At ArcelorMittal we take pride in supporting the Automotive Industry worldwide - it is in our DNA. Every year, more than 10 million tons of our steel are used to produce vehicles worldwide. Steel is the preferred material for the automotive industry, offering the optimal combination in cost, performance, and sustainability and we are constantly improving and innovating to meet the evolving needs and challenges of the industry.
Steel is the dominant material in a car, of which 70% has a composition that did not even exist 20 years ago,
As automotive evolves, and we are committed to helping the automotive industry build a better world with smarter steels, smarter steels have a central role to play in the new world of electrified mobility. Given the inherent strength of these advanced materials, cars today can be both lighter and safer. Steel can also protect batteries, make electric drivetrains more efficient and is endlessly recyclable.
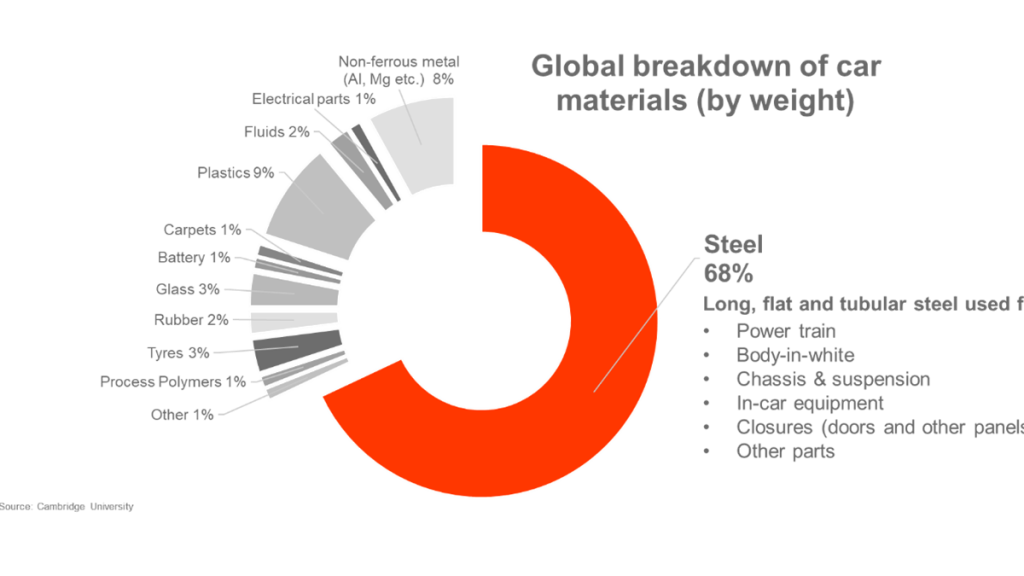
How we help the automotive industry achieve lighter and safer cars …
For a long time, the automotive industry has been driven by the goals of reducing weight and improving safety. We have supported these goals with advanced solutions that we developed in collaboration with OEMs through S-in motion®, our digital suite of generic vehicle designs for each category. We use S-in motion® to discuss, develop and simulate steel solutions with all of the major players in the automotive industry.
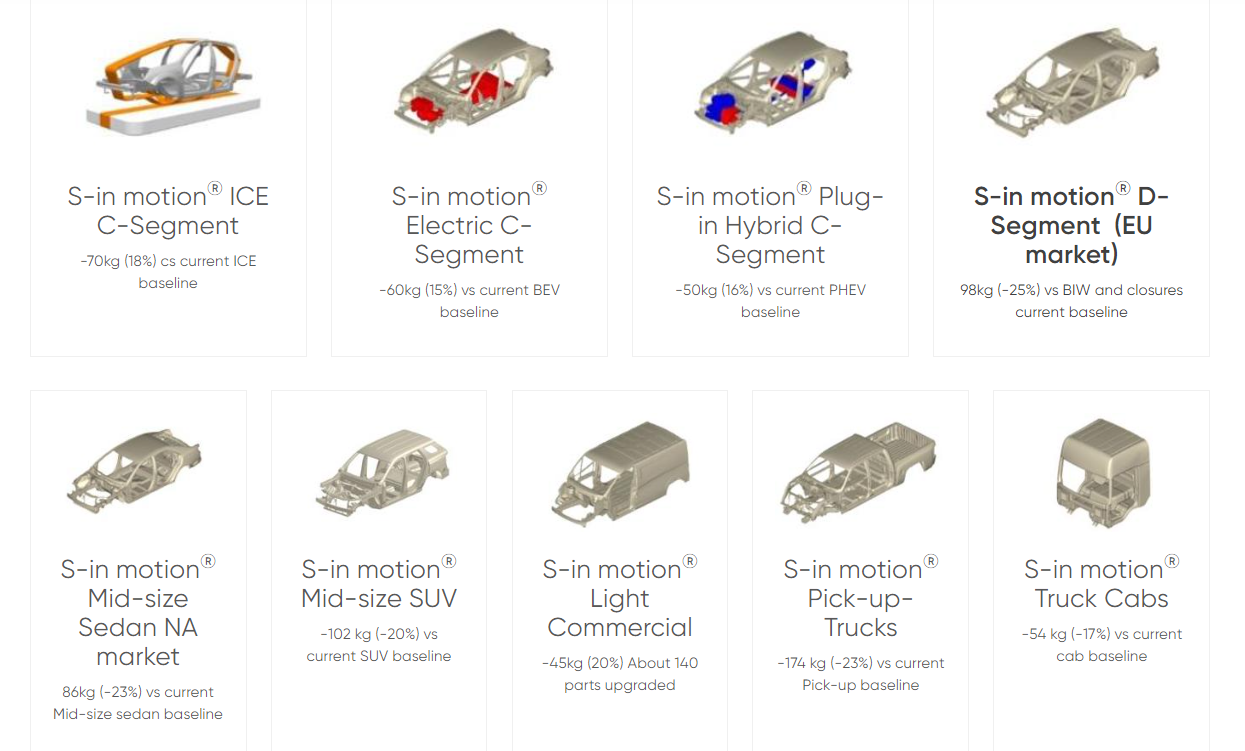
… and now the energy transition challenge
In the new era of energy transition and mobility shift, the automotive industry faces new priorities such as sustainability and simplification. The scope has also expanded to include batteries and electric motors. Our latest innovations, ArcelorMittal Multi Part Integration™ (MPIs) and XCarb™ recycled and renewably produced solutions, combine sustainability and consolidation of parts that save hundreds of spot welds, dozens of robots, factory floor space and assembly time.
3D printing and steel: the right dose of the right material at the right place.
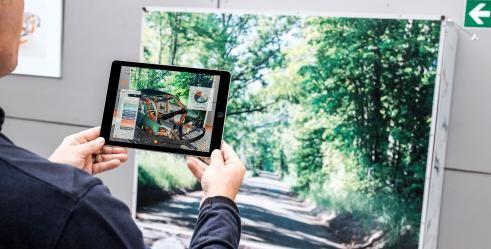
For parts and components, 3rd dimension with Additive Manufacturing now opens more degrees of freedom in design and properties
Today prototyping or short series, tomorrow potentially large series, Steel Additive made parts benefit from Additive Manufacturing Industry constantly pushing boundaries to increase machines throughput and parts sizes translating into parts cost.
Material is the variable left in the equation to optimize further. We are developing and incubating steel powders for 3D printing that can meet the diverse needs and specifications of the automotive industry. We can offer virtually any property with the freedom of design on top.
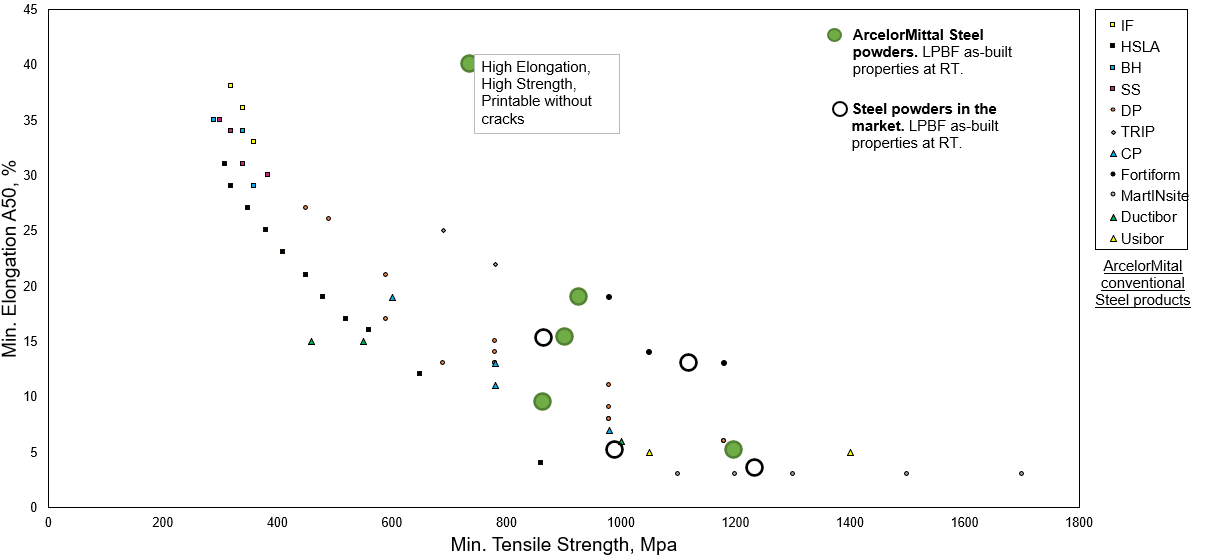
We support the Euro 7 regulation and provide solutions to reduce fine particle emissions from brakes
The first example of adoption of Additive Manufacturing in volumes in the Automotive industry is the answer of OEMs to the new Euro 7 regulation, that extends ruling to brake discs emissions to cut fine particle emissions from discs abrasion. It applies from end of 2026 with more severe steps planned for 2030 and 2035. Emissions from powertrain and exhausts systems were reduced by previous regulations to a point where now particle emissions from brakes become predominant.
Automotive OEMs have developed deposition by mean of Additive Manufacturing of a wear resistant coating on existing grey cast iron discs to meet fine particle emissions targets for friction brakes. The coating process can be done by either high-speed laser cladding or cold spraying, using corrosion resistant stainless steel powder combined with wear resistant carbides.
Following ArcelorMittal’s tradition of improving and innovating to meet the evolving needs and challenges of the industry, the company has set up a lab capability to replicate the coating process and develop further powder solutions that will optimise both the cladding process and the final coating properties, to achieve the best results in reducing brake emissions. ArcelorMittal is poised to address this challenge and is currently working closely with major automotive OEMs and brake manufacturers to improve the solution further.
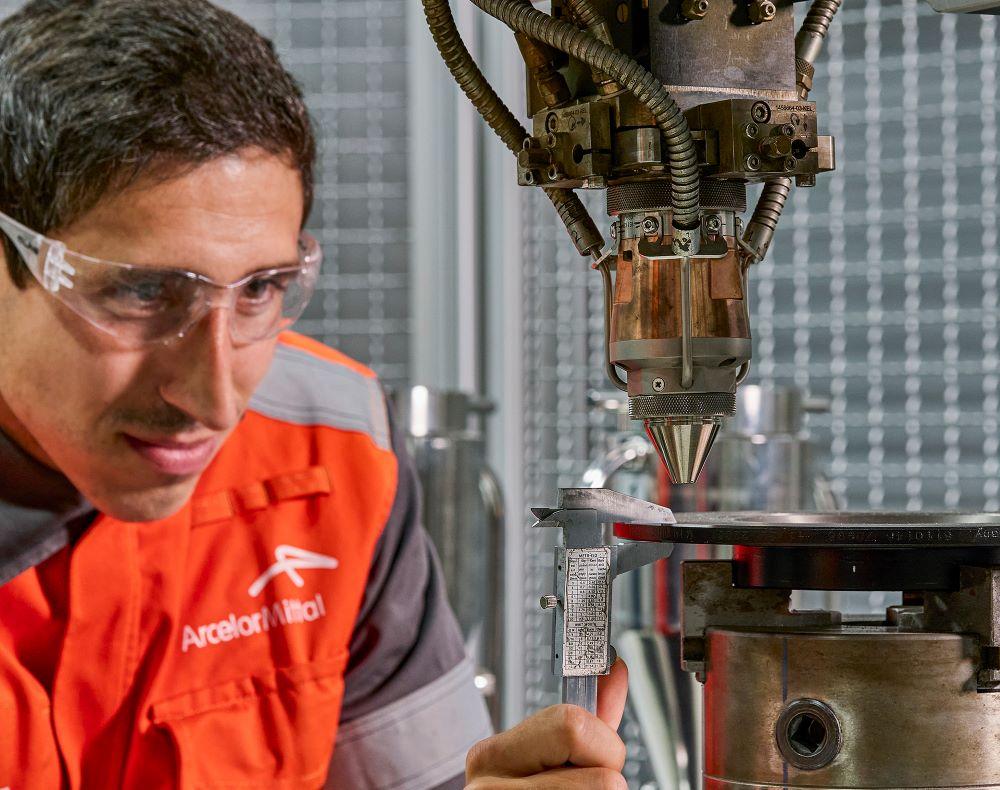
Your co-engineering partner
We are eager to discuss your needs and continue our journey to support the automotive industry with smarter Steel Powders, and also offer services such as DfAM (Design for Additive Manufacturing) and support in improving printing speed to help our customers achieve their goals.