Paris 2024 Olympic and Paralympic Games torch revealed
To manufacture the Torch for the Paris 2024 Games, ArcelorMittal is mobilising its Global R&D department and three of its French sites to represent the expertise of its workforce.
These sites have been carefully selected for their ability to produce steel with a reduced carbon footprint that meets the design requirements of the torch.
At Châteauneuf, ArcelorMittal is casting 100% recycled steel from scrap steel. This chosen route produces steel with a reduced carbon footprint.
The steel is then rolled at Florange, on lines that are usually used for the most demanding products in the automotive and food packaging industries. Finally, the ArcelorMittal site at Woippy cuts the steel sheet into blanks ready for shaping.
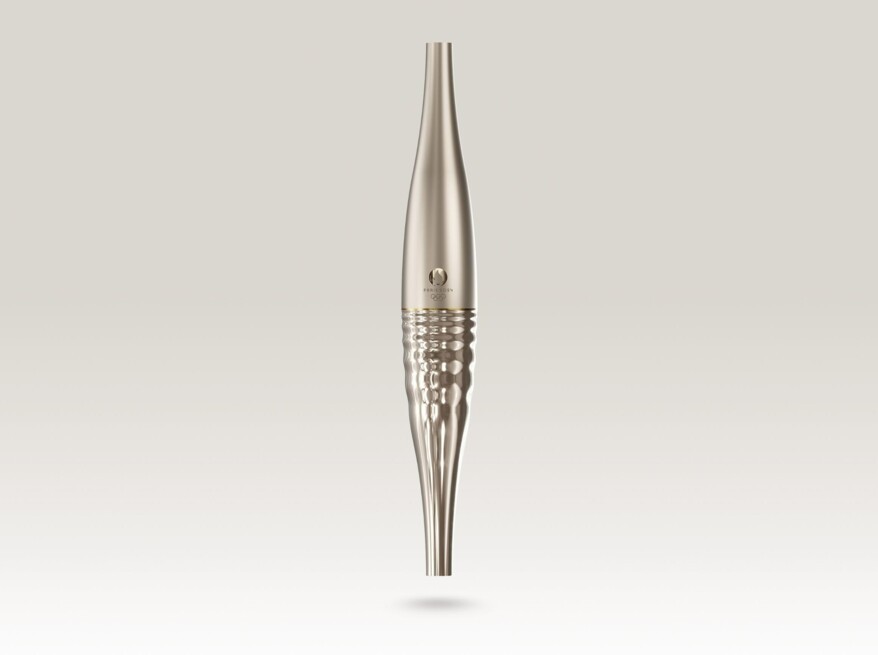
When craftmanship and manufacturing meet
The last two stages of production are carried out by ArcelorMittal's partners, selected for the quality of their work: a famous goldsmith based in Normandy ensures the perfect shaping of the sheets in their factory in Vire to form the top and bottom parts of the Torch. These sections are then sent to a final industrial group, whose role is to apply a high-tech coating to all the steel parts, giving the Torch its characteristic appearance and colour.
Once these operations have been completed, the steel body of the Torch is finished and then ArcelorMittal manages the assembly phase of the body to include the burner and other various parts, particularly those that ensure the Torch's safety of use: in total, there are ten main components that need to be assembled with meticulous care.
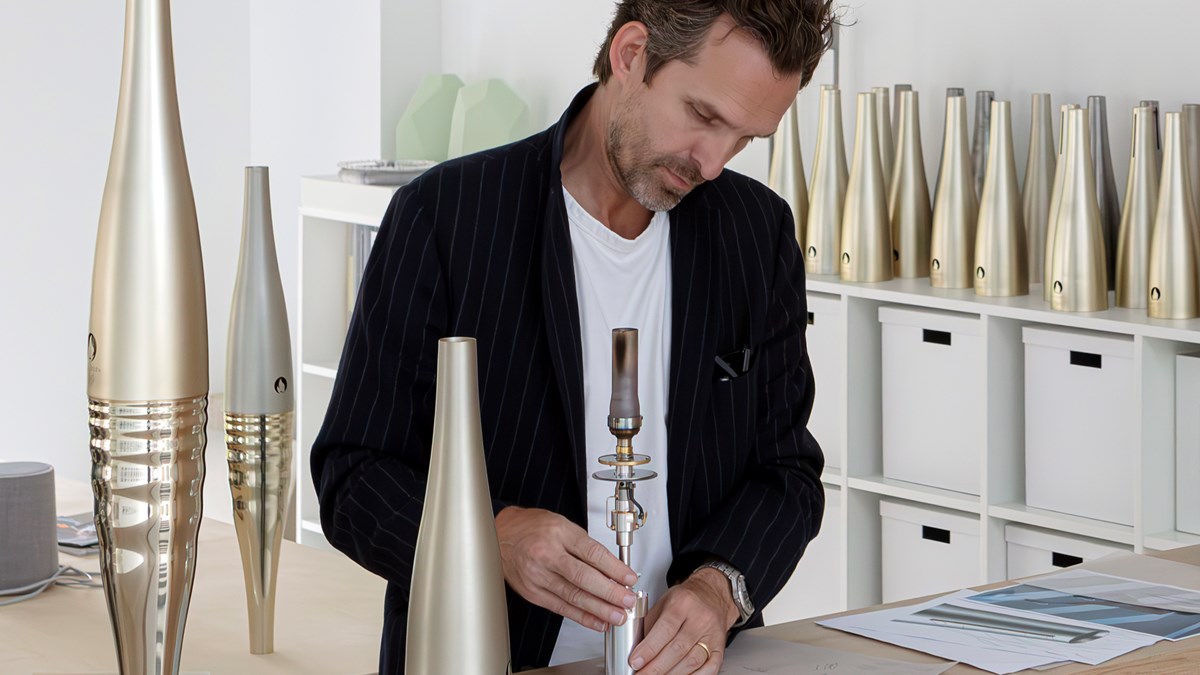
Steel Powders are used in multiple industries and applications
Contact our experts to know how ArcelorMittal Powders can help you boost your productivity!